Five Major Benefits Of Using PCD-Based Tools For Your Manufacturing Processes
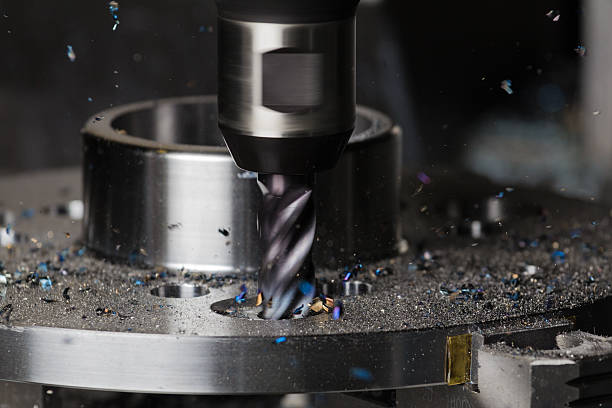
When it comes to precision manufacturing or cutting different metals polycrystalline diamond tools (PCD Tools) are some of the most valuable tools in the trade. PCD tools are the best choice if you are looking for a long-lasting solution that is able to cut more quickly to ensure precision in large numbers.
These are the benefits of using PCD equipment in manufacturing processes.
1. Amazing Tenacity
Based on the way solid cbn inserts is a way to make them impervious to abrasion and wear and tear. The toughness, durability and strength of polycrystalline diamond make it perfect for the use of non-ferrous substances like copper, aluminum alloys, titanium, carbon fiber, platinum and polycarbonate. This makes a PCD round tool the perfect tool to machine a large number of holes in high-volume applications.
2. PCD Tools Offer Greater Dimensional Accuracy for Precision Metal Finishing
Surface finishing is a key procedure for manufacturers of metal. It provides your metal products with an elegant and smooth appearance. Methods for finishing surfaces such as honing, deburring, grinding, as well as glass bead blasting can be costly and time-intensive. PCD tooling allows for greater precision and precision and produces sharper edges with more dimensional accuracy. This results in smoother surface finishes for your metal items. It is not necessary to employ secondary finishing methods when using PCD solutions for metal products. This will save you time and money.
3. PCD Tools have faster Feed Rates
PCD tooling is more effective than other hole-making or finishing options. In fact, they're often ten times faster than traditional tools. It is possible to finish more components at higher speeds without compromising quality. You'll be able to enjoy optimal performance for longer durations of time due to the fact that pcd reamer cutting speed is a high wear resistance. Because of their high efficiency that sundi tools has, you'll be able to take on more work, and yet still get perfect surfaces.
4. PCD Tools Have a Long Cutting Lifetime
PCD tools have a longer time to use compared to other types of cutting instruments. While other cutting tools can last for several weeks based on the level of usage, PCD tools will last for much longer. This means that your production will not be affected by long downtimes while you look for replacement tools. You'll save both replacement and operational costs by using PCD solutions. This can ultimately improve your work efficiency and ROI. Another reason why PCD tooling is an ideal solution for high-volume manufacturing.
5. PCD Tools ensure high quality products that are consistent
Because pcd reamer combination are highly resistant to abrasions and wear, they'll remain in good condition for a long period of time. Therefore, your products will have a consistent top-quality finish. This will allow you to offer your customers quality products on a regular basis. When you use PCD technology, you are providing your process with a tool that is made at top quality and will perform for a long duration.
You can use PCD tools to machine aluminum and alloys, tungsten carbide, copper alloys, laminate floors glass fiber, ceramics, carbon fiber, and graphite. Polycrystalline diamond is efficient in the production of. For the finest quality of PCD tools, get them from reputable professionals in the field of finishing and tooling near you.