Five Factors That Can Increase Carbide Punch Tool's Profitability And Lifetime
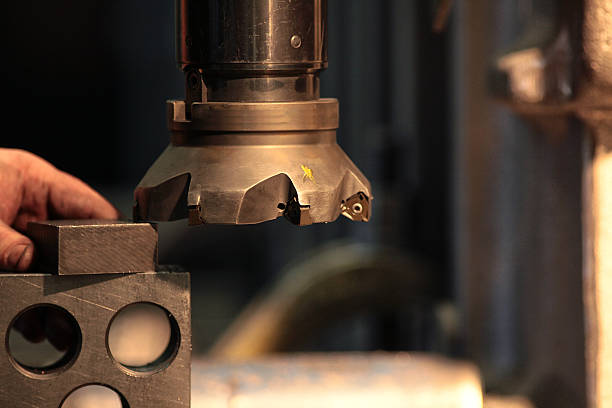
Five elements can boost the life of your tool, increase profitability, and ensure fabricators get the best out of their precision tools, prevent wear and ensure they punch the correct designs.
These five tips will help you get the most from your punching tool.
Proper Positioning
One of the most common mistakes fabricators make is not ensuring their turrets are aligned and in good working order not just in terms of position but also angularly towards what is being punched. Saw-toothing can happen when a station isn't aligned correctly and it is turned by half an inch. This can be caused through the use of a nipper or making straight lines using the use of a rectangular tool. This saw-tooth effect may cause uneven wear on the tool as time passes, which can eventually result in a loss of cutting edge.
Nibbling can cause side loading where the punch starts to come down and only a portion of the tool is able to penetrate the material. The majority of the tool is left unsupported, which makes the tool pull towards the side that is not supported and cause a break in the sundi tools.
If you intend to nibble, professionals suggest using fully guided tool with the stripper that is designed with a tighter clearance to keep the precise carbide punch point in a straight line when it is penetrating the sheet. This is especially useful to make tiny holes in thick materials as well as nibbling.
Coatings and treatments
Treatments and coatings are great methods to extend the life of your punch and reduce the risk of galling. One of the best ways to get the most from your punching device is by coating. There are many choices for coatings and treatments, which include a nitride treatment that infuses with nitride the punching points.
This helps make the punch more slippery as it's punching through and pulling out of the material. Coatings like zirconium, titanium and nitride can be applied in thin, multiple layers onto the punch point. This provides lubricity to the point of the punch and keeps it cooler in high-hitting applications where heat buildup can occur.
Right Pass Away Clearance
The correct clearance is vital as it has a massive bearing on the stress factor on the tooling as well as the surface finish of the hole itself.
Burrs are a sign that your die clearance is not correct. A lack of clearance could cause the material to roll and stretch, creating either the appearance of a down-edge or a burr. If the clearance is too tight, this can cause extreme stress on the tool which can cause the punch to pull out of the pierced hole.
Proper die clearance results in more efficient stripping and less burr. Die clearance is dependent on the material. With stainless, fabricators would typically adjust the die clearance to 25 percent of the thickness of the material. The die clearance for mild steel and some varieties of aluminum is approximately 20% less than that of stainless. It depends on the material being punched.
4.Sharp Tools
A sharp tool can make a an enormous difference in the performance of your holes for punching. It's the easiest way to feel your tool to tell if it needs to be sharpened. If your tool feels dull, it needs to be sharpened. you can also tell by the shape of the hole, if there's an overhang on the edge of the punch this could indicate an unusable tool. A hole that is not straight could indicate the punch being broken down. A hole that appears egg-shaped, for example, could indicate the punch is beginning to break down.
It's easy to discern the difference between a punched that hits a sheet and dull ones. Fabricators must be able to sharpen their tools frequently, rather than just punching until they become very dull.
Sharpening your tool more frequently and taking out more material every time is more effective. This can dramatically improve the tool's life expectancy. Sharpening tools more often can improve progressive punch, tool life by side-by-side testing.
To sharpen your tool, a good coolant is essential. You can damage the tool if you don't use coolant when you are sharpening. Use a high-quality grinding wheel with consistent speed to bring the tool in.
When you've finished sharpening your tools, it's essential to de
-magnetize them. As they become magnetic they will attract carbon-based debris. Any dust or other debris on the tool increases the amount of wear. You are essentially punching through additional garbage.
There may be a burr around the edge of the point after tool sharpening. Make use of a soft abrasive remove the material. It will leave a clean edge with a minimal radius. After sharpening the dies, be sure you use die shims. This will ensure that the dies are of the right level so that the punch is able to penetrate all over the board.
Lubrication
Fabricators might not properly lubricate their punches. This can cause an increase in the life of the tool by as much as 60% and cause galling when working with materials that are soft. A properly lubricated tip can stop the tool from heating up.
Five points that are crucial. You must ensure that your dies and tools carbide punches are stored properly to prevent them from rolling around or being damaged.