CNC Machining Offers Many Advantages Over Conventional Methods
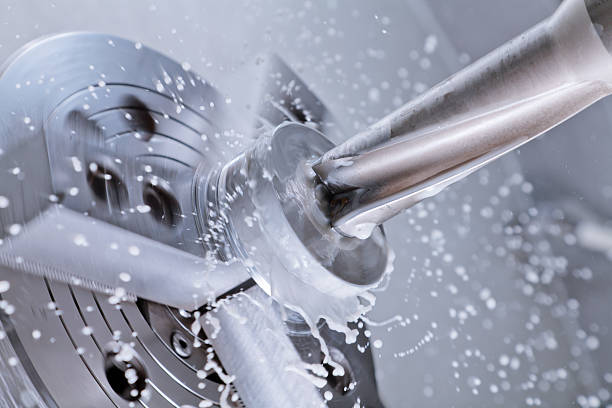
Computer-numerical control (CNC CNC machining) is an essential component of the manufacturing industry. This is the case for operations that used engineer-operated equipment such as routers, shaping machines, and center lathes. Equipment that requires operator involvement can be completely replaced due to the numerous CNC benefits of a machine. Manufacturers of all kinds across a variety of industries have chosen the benefits of machine shop for manufacturing and fabrication purposes. It offers speedy, efficient and precise production capabilities that are that is ideal for large-scale production of products normally made using a router, grinder, center lathe, vertical miller, or cutting machine.
Computer-numerical control has certain advantages over traditional methods of production and financial cost. When it comes to manual lathing for instance, there needs to be a qualified technician on every machine, while with CNC machining, a skilled operator can control multiple machines.
CNC machining produces a broad selection of plastic and metal elements that become a part of businesses and the general environment. A lot of industries require accurate precision, precise, and complex cuts.
In the 1940s, U.S. Air Force mechanics developed the first CNC machines. The first machines utilized punched-paper technology as a driver, and that has evolved into today's digital software. CNC manufacturing quickly gained in popularity because of its capability to produce extremely precise results in large quantities for many applications. CNC machineries can be automated to provide consistent, precise results.
Fairlawn Tool is your local expert in CNC Machining. Read on to learn the answers to many common questions we get about this procedure:
What Are CNC Machines?
Computer-numerical control machining is an approach used by manufacturers to produce machines for parts, products, and other things. This is possible because of CNC machines.
A cnc turning is an instrument that uses Computer Numerical Control over
machine tools such as routers, lathes mills, grinders and lathes. Computer
Numerical Control is different from standard PCs due to the kind of software
used to control the machine. The machine is specifically designed and programmed
with G-Code -which is a particular CNC machine language that permits precise
control of features such as speed as well as location, coordination and feed
rate.
Computerized software that is specially designed drives the machining. G-code is a programming language that allows precise control over the coordination, feed rate and speed. The G-code-infused program is housed in the computer, which looks and feels like the sophisticated desktop.
A single programmer can manage machine operations from a computer console. This is comparable to multiple operators operating on lathes, routers, shapers, mills or routers. Computerized, automated machining method can accomplish grabs, holds and other tasks that human operators and conventional machines usually can't perform efficiently.
Are CNC Machining and Conventional better?
CNC machine and conventional machining are both designed to reach the same goal beginning with a piece of plastic or metal, and then shape it into a part. The major distinction is that CNC can be automated, and conventional machining is a manual labor. The major benefits of cnc machinist, over conventional machining include speed, productivity, accuracy.
CNC lets a skilled person to program software to cut the piece. In conventional machining, a knowledgeable worker is in charge of all the steps to setup and operate the machine. When using a manual machine an expert operator also has to make the gears work, while CNC machining does not use gears.
Conventional machining is generally less expensive and is suitable for smaller projects. CNC is usually employed for large-scale projects, and is not as cost-effective for smaller projects.
For example, imagine the components you could imagine. A part requires convex and concave arcs as well as imperial and metric threads and two tapers with different degrees. A CNC machine that is automated uses three tools to cut the part and the traditional machine would require five tools and possibly longer time.