Cone Crusher Liners What To Consider And When To Change
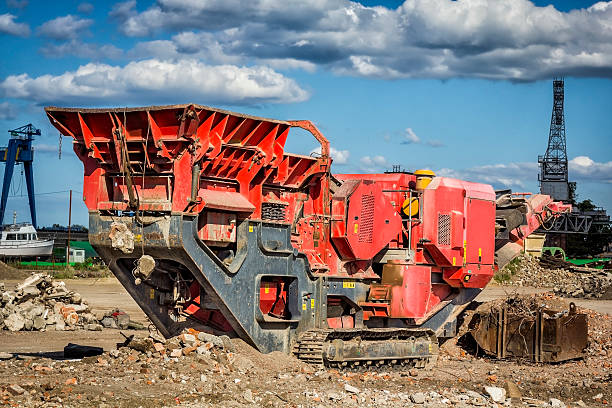
Cone Crushers were created more than century ago to help with secondary, tertiary, and even quaternary material reduction.
Cone Crushers are like other compression crushers. They come with an crushing chamber, or cavity, in which the rock is crushed to a smaller size. The crushing chamber in the Cone Crusher is the space created between the mantle (the moving piece of steel) and concaves (the stationary steel piece). Concaves and mantles are shielded from wear and tear by replaceable manganese liners.
What is the best cone crusher liner
A broad range of liners is available to take in fine and coarse feeds. The one you choose depends on several aspects. The most crucial factor when it comes to Cone Crusher Liners choice is the feed.
You must have a graded feed that is fed into the crushing chamber. A feed that is well-graded is typically described as:
90-100% passing the feed opening on the closed side. Some people also look at the open side, and then choose the smaller one.
40-60% pass the midpoint.
0-10% of the population is passing through the closed-side setting.
Matching the entire feed gradation and not only the feed size is essential so you can make the most out of the chamber. It is crucial to utilize the maximum amount of the crushing chamber as you can to get the required reduction and throughput you want.
Plant feed size and the output of your previous crushing stage determine the maximum feed size, which will give the maximum opening for the cavity. The cavity opening shouldn't be too big in relation to the overall size of your feed. Cavity openings that are larger than feed sizes can lead to inadequate reduction and lines.
The feed size shouldn't be too small. This can result in the majority of the crushing process to be carried out in the lower part of the cavity. If this is the case, the bottom of liner will wear more quickly than the top. Production will drop due to the poor reduction ratio. At a minimal volume level, the crusher's maximum power will be exceeded, and bearing alignment issues could arise.
The majority of wear and tear on Mill Liners Foundry occurs right before the parallel zone (the most narrow space between the mantle and the concaves where the crushing occurs), but this wear will be accentuated if the feed is too small and you'll end up having a bowled-out, swollen pocket prior to the parallel zone is too early.
On the other hand, if the feed size is too fine the feed material is likely to keep flowing within the feed opening which causes the top of liner to wear faster. The feed opening will be closed that reduces throughput and lowers production. The result will be an output that is coarser and be more slabby than cubical. At minimal power draw the limit of volume is exceeded.
Understanding the gradation of your crusher will help you choose the best Shredder Parts configuration, which will satisfy your production needs. A good liner choice will give you a better nip, and allow for more flexibility to alter other parameters like the closed-side setting.